Affordable packaging machine repair service for all types of equipment.
Affordable packaging machine repair service for all types of equipment.
Blog Article
Exactly How Professional Packaging Machine Repair Work Services Decrease Downtime and Boost Productivity
Specialist product packaging equipment repair services are essential in lessening downtime and boosting performance through specialized diagnostics and prompt treatments. The implications of such solutions extend beyond prompt fixings-- unloading the broader impact on operational efficiency exposes essential understandings into lasting efficiency methods.
Relevance of Timely Repair Works
Prompt repairs of packaging equipments are crucial for maintaining operational effectiveness in any type of production setting. When equipment breakdowns or breaks down, it can cause substantial interruptions in assembly line, resulting in increased downtime and shed income. The longer a packaging machine stays out of order, the better the effect on general productivity, potentially causing hold-ups in meeting orders and diminishing customer satisfaction.
Along with the prompt economic implications, delayed repairs can bring about more extensive damage to the machinery. Parts that are not resolved immediately can weaken even more, requiring more costly repair services or complete replacements, which can have been stayed clear of via timely intervention. Furthermore, routine upkeep and timely fixings can enhance the life expectancy of product packaging equipments, making sure that they operate at optimal efficiency levels - packaging machine repair service.
Spending in professional product packaging device repair work solutions is essential for mitigating these dangers. An aggressive strategy to repair services not just keeps production routines however also promotes a society of reliability within the company. By focusing on prompt repairs, companies can maintain their one-upmanship, maximize resource allotment, and ultimately enhance their bottom line with enhanced operational efficiency.
Know-how in Diagnostics
When it comes to keeping the effectiveness of product packaging machines, know-how in diagnostics plays a critical function in identifying problems prior to they escalate right into major failures. Skilled service technicians utilize advanced analysis tools and methods to carry out complete evaluations of equipment performance. This proactive technique enables them to determine the origin of breakdowns, whether they originate from mechanical wear, electric mistakes, or software application inconsistencies.
Effective diagnostics not just promote quick recognition of issues yet likewise enhance the total dependability of packaging operations. By conducting detailed analyses, service technicians can evaluate the health of crucial elements, guaranteeing that even small abnormalities are resolved promptly. This interest to detail lessens the danger of unanticipated breakdowns, which can bring about expensive downtime.
In addition, specialist diagnostics give important insights into operational fads, permitting companies to make educated choices pertaining to devices upgrades or alterations. By leveraging these insights, business can optimize their product packaging processes, leading to improved efficiency and productivity. Inevitably, buying analysis know-how is crucial for companies seeking to keep seamless procedures and support high requirements of high quality in their product packaging processes.
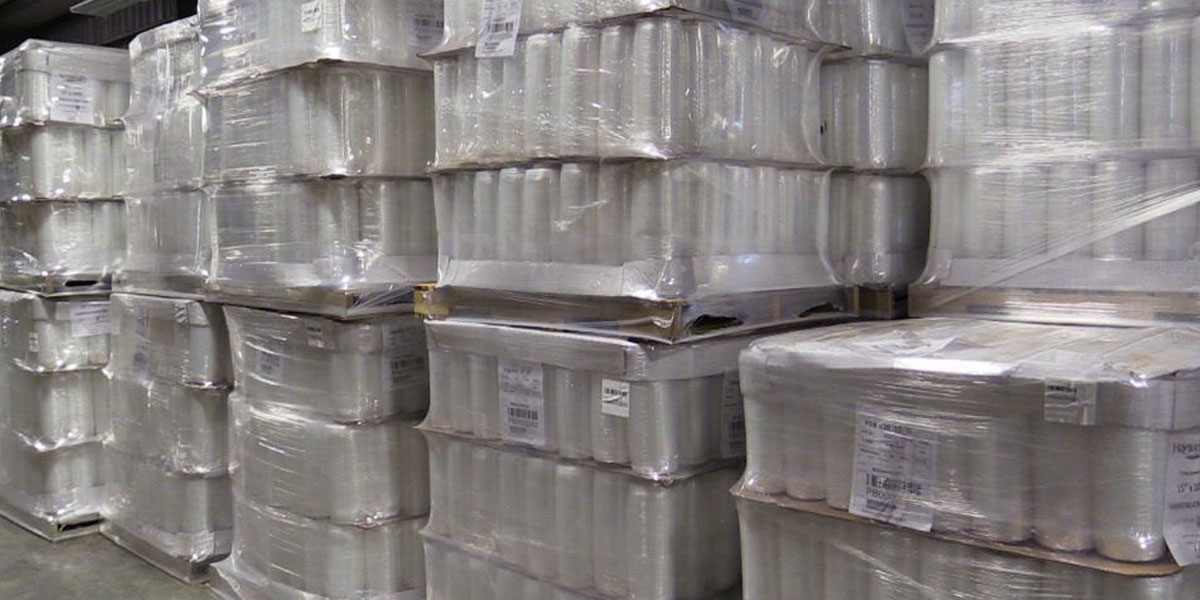
Preventive Maintenance Conveniences
Preventive maintenance matches expert diagnostics by proactively dealing with potential concerns prior to they manifest right into severe problems. By executing an organized precautionary upkeep program, business can considerably decrease the threat of unexpected maker failures, thereby decreasing costly downtime. Routine evaluations, cleaning, and parts substitute aid make certain that product packaging machinery operates at optimum effectiveness.
One of the vital advantages of precautionary upkeep is its ability to prolong the life-span of tools. By on a regular basis keeping equipment, businesses can prevent the intensifying effects of wear and tear that typically lead to significant repair work or replacements. This not just conserves funding yet also boosts the overall reliability of production processes.
Additionally, precautionary upkeep adds to enhanced safety and security problems within the work environment. By identifying and fixing possible threats before they rise, companies develop a more secure setting for their workers (packaging machine repair service). This proactive technique not only safeguards workers however additionally cultivates a society of responsibility and vigilance

Customized Service Solutions
Acknowledging the distinct demands of each service, personalized solution remedies for product packaging equipment fixing offer customized methods that boost functional efficiency. These solutions are developed to address specific obstacles encountered by different markets, guaranteeing that device downtime is decreased and efficiency is see this site optimized.
Expert fixing solutions begin with a thorough assessment of a company's packaging operations. By understanding the certain machinery involved and the demands of the production environment, service technicians can establish a personalized repair and maintenance strategy. This may consist of specialized training for internal team, the application of predictive maintenance technologies, or the arrangement of committed support during height manufacturing times.
Moreover, personalized services can incorporate versatile service arrangements that line up with a firm's functional timetable, enabling repair work to be carried out during off-peak hours. By prioritizing the distinct demands of each company, these bespoke solutions make sure that repair work are not only efficient but also seamlessly integrate into existing workflows.
Eventually, the focus on modification makes it possible for companies to maximize their packaging processes, bring about enhanced integrity and efficiency of machinery, which is essential for maintaining competitive benefit in today's hectic market.
Effect on Overall Efficiency
Customized service solutions not just address certain repair work needs but also play a substantial duty in boosting overall functional efficiency. By More Info giving targeted interventions, expert packaging machine repair service solutions straight lower the regularity and period of tools failures. This proactive technique makes sure that assembly line continue to be functional, reducing disturbances that can result in pricey downtime.
In addition, efficient repair work services add to smoother process, as well-kept machinery runs at ideal performance degrees. When makers operate properly, the top quality of packaged items improves, resulting in fewer issues and much less rework. This improvement not only enhances productivity however also strengthens client satisfaction.
Additionally, normal maintenance and fast feedback times from fixing professionals promote a society of reliability within the organization. Workers can focus on their primary jobs as opposed to bothering with prospective tools breakdowns. As a result, the total throughput of the production process rises, permitting firms to meet demand more successfully.
Inevitably, the calculated investment in expert fixing solutions translates to enhanced effectiveness across all functional elements, making sure that services can adjust and flourish in an open market. This harmony between maintenance and productivity is crucial for lasting success.
Final Thought
In final thought, expert product packaging equipment repair service solutions play a crucial function in lessening downtime and improving performance within making environments. Prompt repair work, expert diagnostics, and preventive upkeep add to the find out here now reliability of tools, while customized solution options deal with details functional needs. The advancing result of these services leads to improved overall performance, enabling companies to maintain production timetables, support product quality, and properly satisfy market needs. Purchasing such services eventually drives continual operational success (packaging machine repair service).
Report this page